
Design, Analysis and Optimization of Chassis for Mobile Robotic Platform for Supermarkets
Problem Statement:
Super markets have narrow space between their shelves, which creates congestion when two or more people want to pass through. Also the waiting time for billing carrying a large shopping cart is inconvenient as a whole. Since lot of people shop in and out all day long, the shopping cart has to be structurally rigid while also being light weight at the same time.
Goal:
-
To design and analysis of electric motor-powered compact trolley chassis with high strength to weight ratio.
-
To make comparisons among the suitable martials and select the best one for the design and purpose based on Ashby charts
-
Modal analysis to avoid resonance
Approach:
-
Design of cart using space frame structure & static structural analysis with boundary conditions including payload of 20kg
-
Calculate performance index in terms of stress, density & cost of material
-
Optimizing the dimensions of cross-section to have deformation less than 0.5mm while minimizing the mass of chassis as well
Results:
-
The calculated reaction force for front and rear wheels are 125.33N and 131.44N respectively.
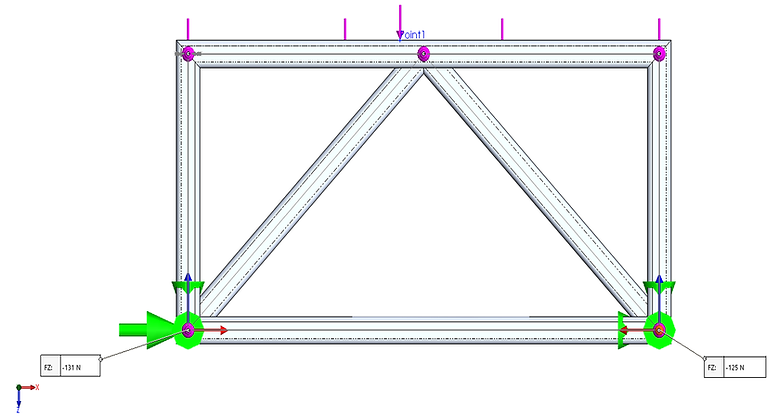

-
Of the different types of cross-sections, hollow square tubes was selected for this application as it had the highest area moment of inertia of 7872mm
-
Beam elements were used and mesh convergence from 10mm to 4.5mm for top members, 10mm to 6.5mm for side members (5% convergence)
-
Materials for Analysis: ABS, Alloy steel, Aluminum 6061-T6, Fiber Composite(Kevlar), Wood(mahogany). The performance index is given as the ratio of density to yield strength as below
​
​
​
​
-
The performance index for materials is calculated in Table 5 and it is found that Aluminum 6063-T6 is the best material for the application as it has the highest performance index when cost is considered

-
The vibration inducing part of the cart is the motor, which creates vibration at 3.33Hz. the modal analysis yields the 1st and 2nd mode as 41.71Hz and 48.82Hz respectively.
-
We can conclude that the design is safe from resonance since the disturbance frequency is too low when compared to the first natural frequency.

Stress: Al 6061-T6

Deformation: Al 6061-T6
Tools Utilized:
-
Solid works
-
Ashby charts
-
Optimization
-
Modal analysis